ABB and Treston developed a cobot trolley together - collaboration started at the Subcontracting Fair
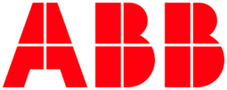
We interviewed Juha Mainio from ABB about the collaboration and the latest news in cobotics.
Cobots and flexible automation are here to stay
Juha Mainio has been working at ABB for about twenty years, with a focus on cobots since 2016. That year marked the launch of ABB’s first dual-arm cobot, YuMi.
“It was a big deal, and we saw lots of different use cases for cobots. Since then, ABB has systematically increased its investment in the development of new cobot solutions,” says Juha, who now works as Regional Sales Manager at the Finland’s Robotics unit. Globally, ABB’s Robotics unit employs 11,000 people.
According to Juha, cobots are here to stay and are not just a passing trend. The numbers of cobots are increasing year by year, but the most significant growth is yet to come. “Industrial robots are not disappearing, but in addition to them, cobots, as well as autonomous mobile robots, have become more common. They complement each other well, creating flexible automation. Cobots are what we call ‘entry level’ robotics, which means that they are easy to implement even in small and medium-sized enterprises that do not necessarily possess specific expertise in robotics.”
The development of the cobot trolley was seamless

From the beginning, Juha had a positive feeling about the collaboration with Treston. “I had come across Treston both at customer sites and in schools where I’d been training people on cobotics, so I was somewhat familiar with Treston’s solutions. Treston has a strong, high-quality brand.”
Both Treston and ABB had representatives from product development, marketing, and sales participating collaboration.
“The collaboration was seamless, relaxed and professional,” says Juha, recalling the project. The early stages of the project involved discussions on customer needs, applications and possible joint development projects. This led to the idea of a cobot trolley, which could easily serve the needs of multiple workstations and speed up the return on investment.
Kimmo Lehti, Director of the Products unit at Treston, was also involved in the development work. “Ideas were refined through practical testing. For example, instead of mounting the trolley via the back attachment to the workbench, we opted for side attachment. As a result, we provided ABB with a prototype of a cobot trolley, which we tested in ABB Drives unit,” says Kimmo Lehti, explaining the different phases of the collaboration.
Most compelling cobot applications
Over the years, Juha has realized which applications are particularly suitable for cobots. Through customer visits, he has also discovered what makes cobots attractive to a wider audience.
“In recent years, cobots have been used in various applications, such as grinding and polishing. Right now, the most interesting application is welding”, Juha reveals. What the applications have in common is that they improve ergonomics for workers by assisting with ergonomicly challenging tasks or enhancing high-quality operations or safety.
“Working with customers on the factory floor has made it clear that it is not necessarily about acquiring a cobot for a single task but rather using the same device in multiple workstations. That is a recurring theme. That’s why a cobot trolley is more than necessary,” Juha explains.
Making cobots more common
The keyword is ease. “If we want to boost the use of cobots, we need to make them even easier to purchase and deploy,” says Juha Mainio from ABB. Programming and integrating various tools, such as grippers or machine vision, with cobots should be straightforward.
Continuously evolving artificial intelligence (AI) brings fresh cobot application ideas as well. In logistics, for instance, cobots equipped with machine vision can be used to efficiently move and pick up objects. AI-based machine vision solutions are self-learning, which means that each production cycle makes the system more reliable. The machine vision of cobots can be trained to identify features in products, helping to recognize which items need to be unloaded from a pallet. As the cobot continues to work, it keeps learning new things.
Traditional job roles undergoing transformation

Manual industrial tasks will be transformed at the wake of new digital and AI-based applications. However, digitalisation doesn’t translate to fewer jobs. For example, when cobots are used to improve ergonomics, employees’ ability and motivation to work remains high and efficiency is improved. By investing in a new type of work environment, companies are also able to make manual work more attractive to younger generations. Instead of being a threat, a new kind of digital colleague can be appealing to millennials.
According to Juha, cobots are well-suited for a wide range of companies. “As a solution, cobots are both scalable and reliable, and in addition they are suitable for small and medium-sized enterprises seeking assistance in streamlining their production. By improving their production, SMEs can ensure they remain competitive and create new job opportunities.”
The ecosystem is undergoing strong development
The ecosystem around cobots and various new workplace solutions is continuously evolving. Device manufacturers, integrators and customers are all contributing to the development of new solutions. Sharing new ideas and experiences is crucial for the advancement of the industry. ABB is also launching new cobots on the market this summer, featuring increased payload capacity and reach.
Treston, on the other hand, continues to develop solutions that enhance well-being and ergonomics in industrial environments. Therefore, collaborative development projects with entities working with cobots, mobile robots, machine vision, AI, exoskeletons, and various other digital aids will continue actively.
If this inspired you to consider workplace solutions from a new perspective, don’t hesitate to get in touch. Feel free to ask for more information!