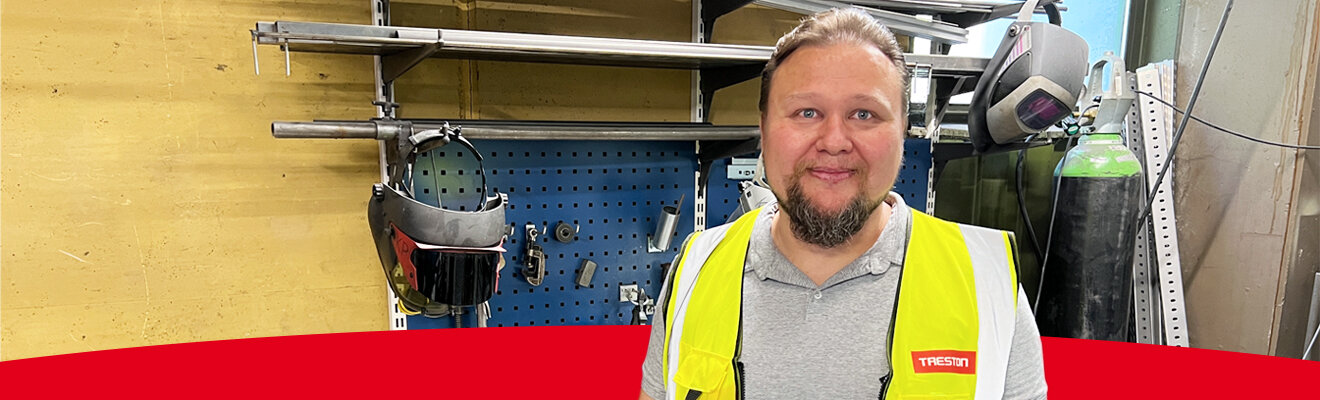
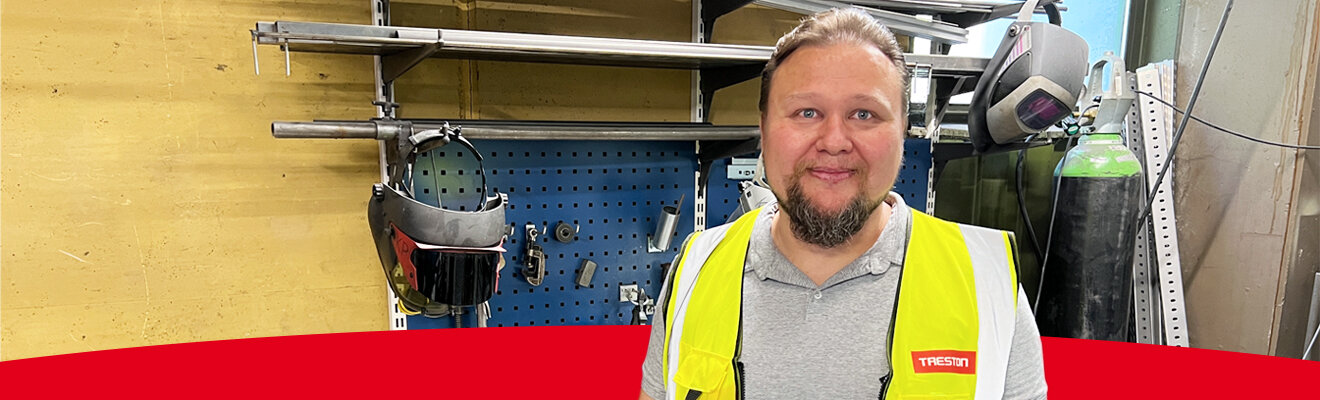
Treston Quick Edge – How was the fastest workbench on the market born?
In this blog post, product development engineer and customised product designer, Kimmo Harjula, and quality controller, Keijo Pihlaja, explain how the Treston Quick Edge became a patented invention that now serves our customers around the world.
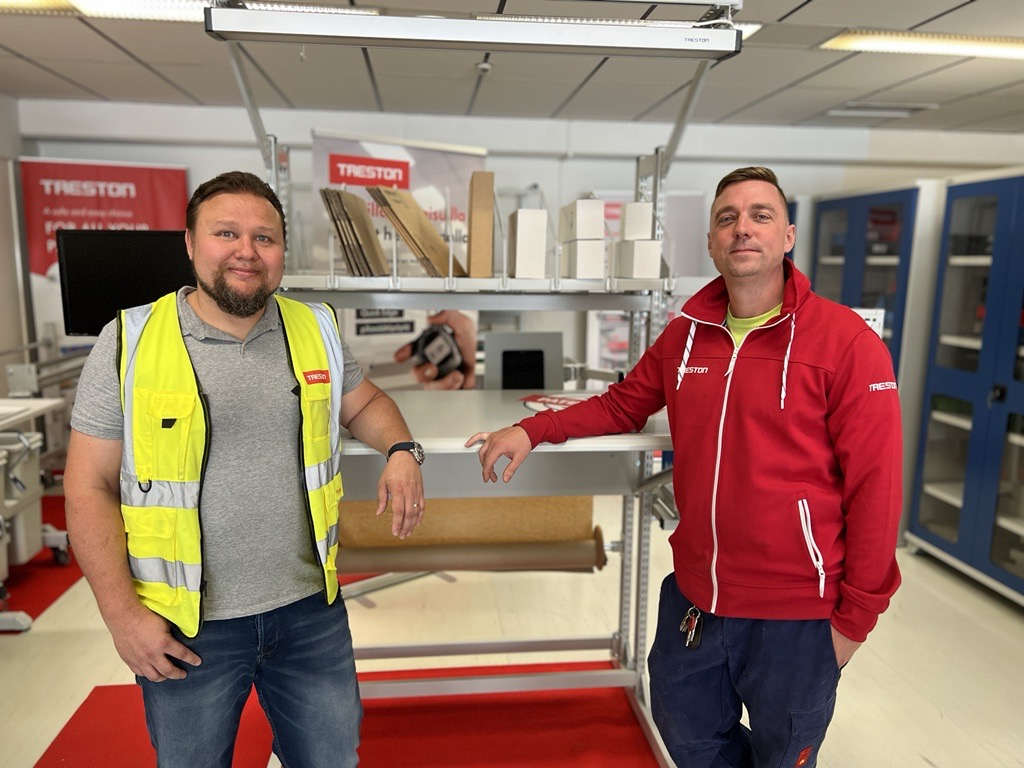
It takes about a minute and a half before the regular electrical workbench is adjusted to the desired level. That's an excessive amount of time to waste
Speed and adjustment range were the deciding factors
An essential part of a smart, ergonomic working environment is a workbench that can be adjusted to the optimal height. The adjustment features are emphasised especially when people of different heights work at the same workstation and the size and weight of the goods to be processed vary during the work shifts. However, you don't always have time to adjust the table to the right height, or the extent of the adjustment range is simply not enough.
A logistics centre had noticed the same thing. Kimmo Harjula, the inventor of the operating principle of the Treston Quick Edge, remembers the beginning of the project: "When the first request for a quote came, I remember that the most important features for the customer were the extent of the desk's adjustment range and the speed of adjustment. At that point, we could offer hand crank, Allen key, or electrically adjustable workbenches, but these options were excluded. The customer wanted to make sure that the adjustment option would actually get used. In the first round of offers, we therefore did not have a suitable solution to offer."
The quality manager, Keijo Pihlaja, who was involved in the project, knows extremely well the kinds of issues customers struggle with: "On a regular electrically adjusted workbench, wide use of the 550 mm adjustment range is quite slow, and the adjustment range is more limited. It takes about a minute and a half before the regular electrical workbench is adjusted to the desired level. That's an excessive amount of time to waste in the logistics centre when it multiplies during the day."
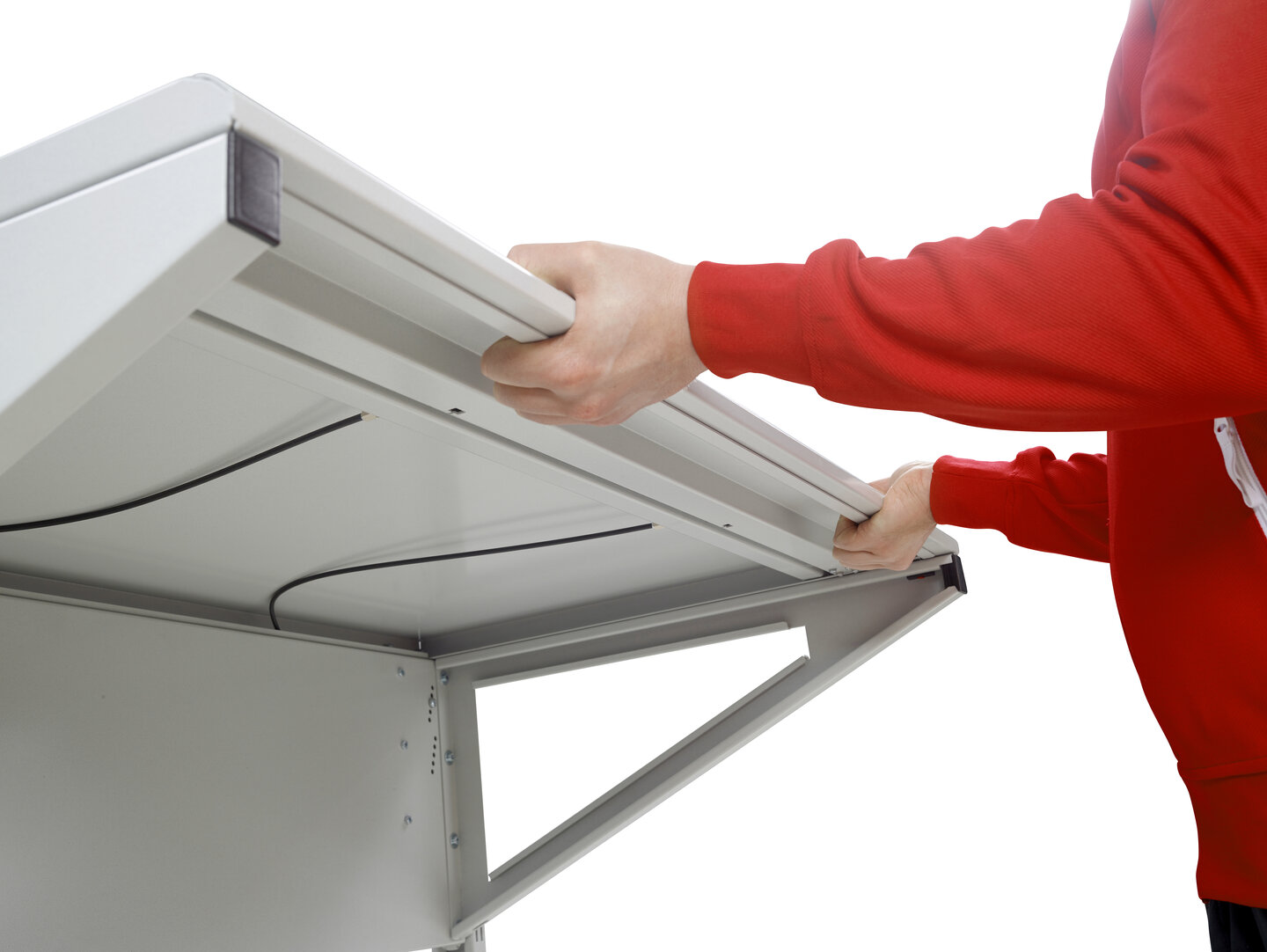
The fact that the raw version worked so well really made us believe that there is an idea here
The new technology worked smoothly
When there was no standard solution to offer, Kimmo started to think about the idea that this could be an opportunity to develop an alternative way of adjusting the workbench for the customer. "We made the first prototype together, and let's just say the look of the first version was pretty hideous, but the technology worked ideally. From there, we started developing it further to match Treston's quality level." Keijo nods and continues: "The fact that the raw version worked so well really made us believe that there is an idea here."
The project team thought about the appearance together, and Kimmo remembers bringing it up: "At first, the appearance was strange because I had thought in my own mind that you shouldn't touch the adjustment uprights. Then, in a project meeting, I brought it up and our ergonomics expert, Jonna Patama, questioned my thoughts. After that, the product took its final shape. Jonna has also given good viewpoints on how to make the product more ergonomic."
The technology is common, but not for workbenches
The technology used in the new workbench is known from many different products. For example, column drills use a similar spring system. Therefore, it is not a completely new invention in itself, but the technology is new for use in workbenches.
Keijo says that Kimmo was behind the original idea: "It was primarily Kimmo’s idea to use this kind of spring system. After that, we started to further develop the idea together."
Kimmo laughs and explains: "Since I was little, my 'problem' has been that I want to pull things to pieces. My poor dad had to watch from the sidelines while I dismantled all technical devices, from tube radios to technical tools, with side cutters. And this is what I have fortunately done to a column drill, too.”
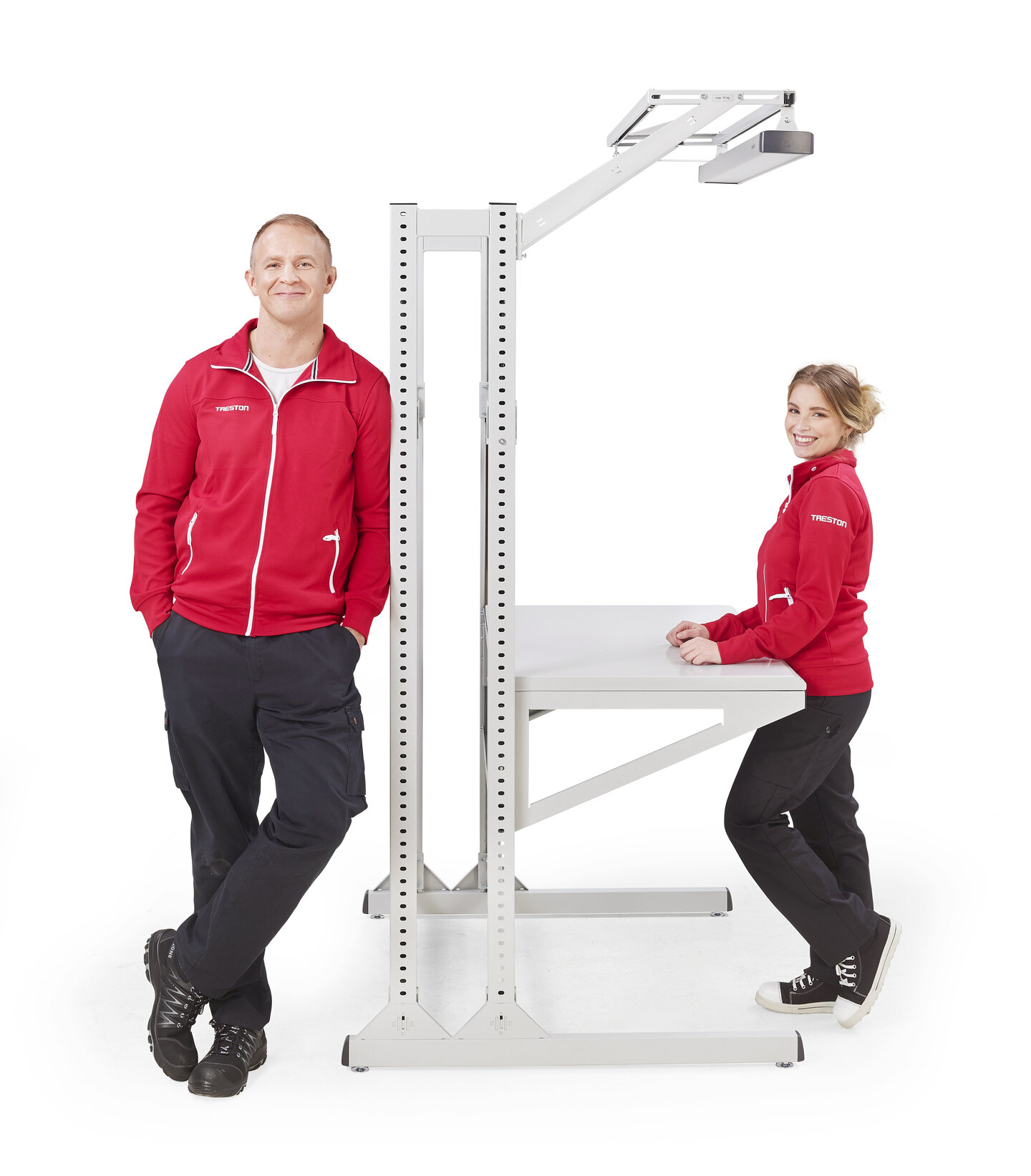
I encourage all designers to be in the production area themselves
The working environment supports problem-solving
Kimmo became part of Treston's product development team about four years ago. He is a well-liked person in the workplace and receives positive feedback from Keijo: "Kimmo joining the design team has brought us a lot of new perspectives. Kimmo knows how to think about product development outside the box. You can tell when a designer knows how to do things himself, too. When you have practical experience, then you also understand how it makes the most sense to implement things."
Kimmo smiles and tells the secret of his design work: "I really like to break boundaries, and Keijo has been a very good partner in that sense. And the factory crew, as well. I encourage all designers to be in the production area themselves. When you walk around here at the factory and involve dozens of brains in thinking about a problem, a solution is much more likely to be found than trying to figure it out alone at home."